One of the most effective strategies for enhancing the properties of injected plastics is the addition of certain additives, as we have discussed in another one of our blogs. Another alternative is the use of fillers. These not only improve the mechanical and aesthetic characteristics of the final products but also optimize costs and promote sustainability. Fillers also reduce the density of the product, resulting in lighter parts.

Next, we delve deeper into the types of fillers, with a special focus on reinforcement fibers, present practical cases, and explore the advantages and considerations of their use.
Filler selection criteria
For selecting fillers to use in plastic injection, it is crucial to consider several key factors:
- Optimal size and distribution of particles: The size of the particles has a direct impact on the material’s viscosity and the maximum amount of filler that can be incorporated into the polymer without negatively affecting its properties. A uniform distribution ensures better integration of the filler into the base material.
- Catalytic activity of the filler surface: The surface properties of the filler can significantly influence chemical reactions during the processing of the plastic. Fillers with high catalytic activity can enhance or modify the properties of the resulting polymer.
- Dispersion and anchoring in the polymer: It is essential that the filler particles are homogeneously distributed and properly anchored in the polymer matrix. Good dispersion ensures the uniformity of the composite material, which translates into improved and consistent properties of the final product.
- Abrasion of the filler in the processing machines: The durability of injection molding equipment can be affected by the abrasiveness of the fillers used. Materials such as carbon and glass fibers, although they provide excellent mechanical improvements, can cause significant wear on the spindle and other components of the injection machines. Therefore, it is crucial to calculate and balance the amount of these fillers to minimize equipment wear.
Particle geometry
The properties of fillers also vary according to the geometry of the particles:
- Spherical: These particles have a high density and offer low viscosity, which allows for a uniform distribution of stresses in the material.
- Cubic or tabular: Excellent for providing reinforcement and efficient packing within the polymer.
- Dendritic: Characterized by their large interaction surface, which improves adhesion and cohesion in the composite.
- Lamellar: With large reflective surfaces, these particles orient well and offer low permeability to gases and liquids.
- Elongated: Provide superior reinforcement and reduce thermal contraction and expansion of the material.
- Irregular: Although they have no special advantages, they are easy to produce and economical.
Filler types
Mineral fillers
Talc (Calcium Carbonate)
Industrial talc (calcium carbonate) improves the stiffness and creep behavior of polypropylenes. Additionally, another advantage of its use is the reduction of sink marks in the piece. A clear example of its use could be interior furniture. However, they tend to be whitish products as talc can cause the appearance of superficial white particles.

Aluminum Trioxide (Alumina)
Aluminum trioxide, more commonly known as alumina, is a compound obtained from bauxite, an abundant mineral in the Earth’s crust.
Technical Properties:
- High hardness and abrasion resistance: Alumina is extremely hard, making it suitable for applications requiring wear resistance.
- Good thermal stability and corrosion resistance: Maintains its structural integrity and resistance in high-temperature environments and chemical exposure.
- Moderate thermal conductivity: Efficiently transfers heat, which is useful in applications where heat dissipation is needed.
Practical Applications:
- Electronic Components: Used in casings and heat sinks in electronic devices, providing protection and efficient thermal management.
Graphite
Graphite is a natural form of carbon, known for its layered structure that gives it unique properties. Graphite is found in both amorphous and crystalline forms, the latter offering better characteristics for industrial applications due to its purity and orderly structure.
Technical Properties:
- Low friction and high lubricity: The layered structure of graphite allows the layers to easily slide over each other, reducing friction.
- Good electrical and thermal conductivity: Capable of efficiently conducting heat and electricity, which makes it valuable in applications requiring heat dissipation.
- Wear resistance and high thermal stability: Maintains its integrity under extreme wear conditions and high temperatures.
Practical Applications:
- Gaskets and Seals: Used in pumps and valves to improve durability and reduce friction, increasing efficiency and the lifespan of these components.
PTFE (Polytetrafluoroethylene)
PTFE is derived from ethylene through a polymerization process. It is a highly crystalline polymer composed exclusively of carbon and fluorine, giving it unique properties.
Technical Properties:
- Excellent chemical and thermal resistance: PTFE is virtually inert to most chemicals and maintains its stability across a wide range of temperatures.
- Low coefficient of friction: Its surface is extremely smooth, which reduces friction in applications involving movement.
- Non-sticky and moisture-resistant surface: Materials do not adhere to its surface, making it ideal for applications where cleanliness and non-adhesion are crucial.
Practical Applications:
- Non-stick Coatings: Used on the surfaces of kitchen utensils and in industrial equipment such as 3D printers to prevent material adherence and facilitate cleaning.
- Medical Components: Used in casings and other medical devices that require low friction and biocompatibility, enhancing safety and comfort for patients.
Molybdenum disulfide
Molybdenum disulfide (MoS2) is a mineral compound found in nature, mainly in molybdenite, the most common mineral of molybdenum. Its lamellar structure similar to graphite gives it exceptional lubricating properties.
Technical Properties:
- High load capacity and wear resistance: Provides excellent protection against wear even under high loads.
- Good thermal stability and resistance to oxidation: Maintains its properties at high temperatures and does not oxidize easily.
- Excellent lubrication under extreme conditions: Works efficiently in high temperature, high pressure, and vacuum environments.
Practical Applications:
- Seals and Gaskets: Used in seals and gaskets to improve durability and reduce friction, thereby enhancing the efficiency and lifespan of these components.
Silicates
Silicates are abundant minerals in the Earth’s crust, primarily composed of silicon and oxygen. These compounds are found in various forms, from sands and clays to quartz crystals, and are mined from natural deposits worldwide. Their unique chemical structure makes them extremely useful in various industrial applications, especially in enhancing plastic materials.
Technical Properties:
- Mechanical and thermal resistance: Silicates provide a significant improvement in material durability and stability.
- Barrier properties: Act effectively as barriers against gases and liquids, making packaging waterproof.
- Chemical and thermal stability: Maintain their properties under adverse chemical and thermal conditions.
Practical Applications:
- Packaging: Used in the production of films and coatings that need to provide an effective barrier against moisture and gases, thereby improving the conservation and protection of packaged products.
Reinforcement fibers
Glass fibers
Glass fibers are produced from various types of glass, mainly silica glass, which are melted and then extruded into fine strands. Glass fibers are valued for their combination of lightness and high strength.
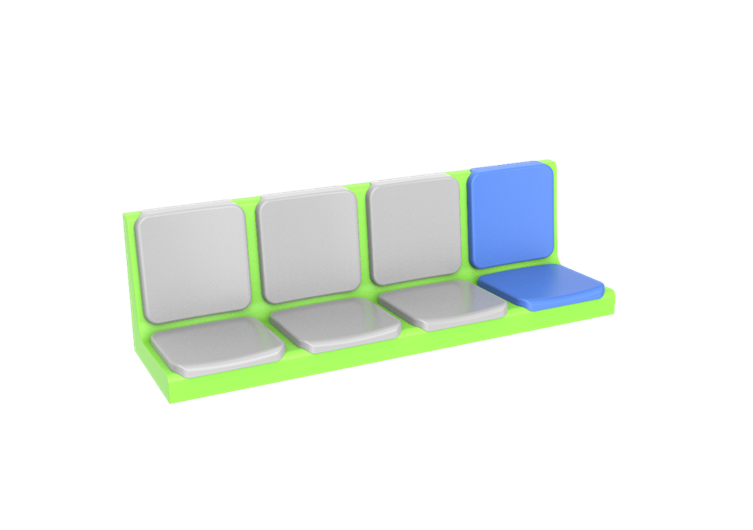
Technical Properties:
- Improvement of mechanical strength: Increases the durability and robustness of composite materials.
- Dimensional stability: Reduces deformation and thermal expansion, maintaining the precise dimensions of the final product.
- Flame retardant: Contributes to the fire resistance of the composite material.
Practical Applications:
- Urban Equipment Components: Benches and panels in bus waiting areas made with polyamide reinforced with glass fiber, offering durability and resistance to urban wear.
- Urban Furniture for Parks and Gardens: Picnic tables and other furniture that require low maintenance and high durability, ensuring a long lifespan even under adverse environmental conditions.
Carbon fibers
Carbon fibers are produced from organic materials such as polyacrylonitrile (PAN), pitch, or cellulose through a carbonization process. This process involves subjecting the precursor material to high temperatures in an inert environment, which removes non-carbon elements and leaves a carbon-rich structure. Carbon fibers are valued for their high strength-to-weight ratio and stiffness.
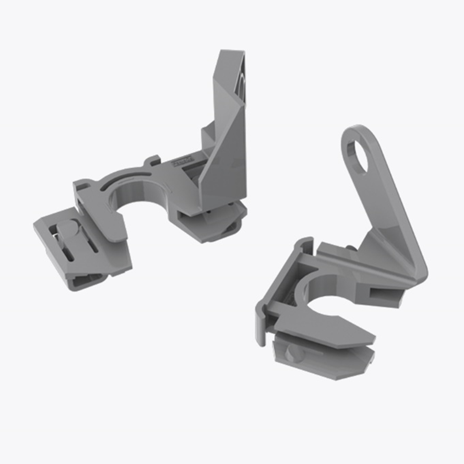
Technical Properties:
- Exceptional strength: Provides high tensile strength, surpassing many other materials.
- High stiffness: Increases the stiffness of the composite material, improving its ability to withstand loads without deforming.
- Reduced material weight: Offers the same or better mechanical properties as other materials but with less weight.
Practical Applications:
- Recreation Items: Kayak paddles and tennis rackets that benefit from the lightness and high strength of polymers reinforced with carbon fiber.
ORGANIC FILLERS
Wood fiber
Wood fiber is obtained from wood processing residues such as sawing or paper pulp production. This type of filler not only provides aesthetic and textural benefits but is also a sustainable option, as it uses renewable resources and reduces the carbon footprint of the final product.
Technical Properties:
- Aesthetic improvements: Provides a natural appearance and a pleasant texture to the material.
- Tactile quality: Improves the touch sensation of the final product, making it feel warmer and more natural.
- Sustainability: Reduces the carbon footprint by using renewable materials and leveraging industrial waste.
Practical Applications:
- Consumer Electronics Components: Casings for electronic devices such as radios and speakers, where aesthetics and sustainability are important.
- Eco-friendly Furniture: Manufacturing of decorative and functional furniture for interiors seeking a natural and sustainable aesthetic.
At Moldblade, we enhance the properties of injected plastics through the use of various fillers, such as minerals, fibers, and organic options. These solutions make our products stronger, lighter, and more sustainable, optimizing performance and manufacturing process efficiency. Our commitment to innovation and quality allows us to offer plastic materials tailored to the needs of today’s market.
- Moldblade y Tragsa. Proyecto conjunto para modernizar el control de riego en la zona del Zújar.
- Insertos Sinterizados: Innovación en la Refrigeración de Moldes de Inyección
- Optimización de Sistemas de Expulsión en Moldes de Inyección de Plásticos
- Parámetros en la inyección de materiales plásticos. Diagramas PVT